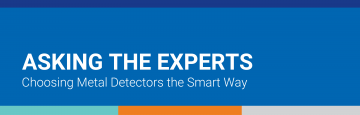
Metal detectors are an integral part of any production process in the food, industrial, scientific, manufacturing, and healthcare industries. The growing demands contributed by changing customer requirements, evolving regulatory and legislative bodies, and stricter industry standards, have put a heavier emphasis on the importance of efficient and effective product inspection in the production and distribution process.
However, merely introducing metal detectors into your product inspection regimen won’t be enough to ensure precise metal contaminant inspection. Performance, sensitivity, and useful life of metal detectors are highly dependent on many factors, including regular maintenance and proper operation to name a few. This is why selecting the right metal detectors for your facility will bring you that much closer to eliminating the occurrence of metal contamination.
WHEN SENSITIVITY ISN'T ENOUGH
First time metal detector shoppers will often come up with a list of ideal features and then go around from brand to brand comparing prices and functionalities without truly understanding what each feature will be used for.
The trouble with this is that many modern metal detectors already come with a long laundry list of features, but these capabilities may not actually improve a production line’s overall effectiveness. So in the end, would-be metal detector owners go for equipment with the longest features list that also falls within their budget.
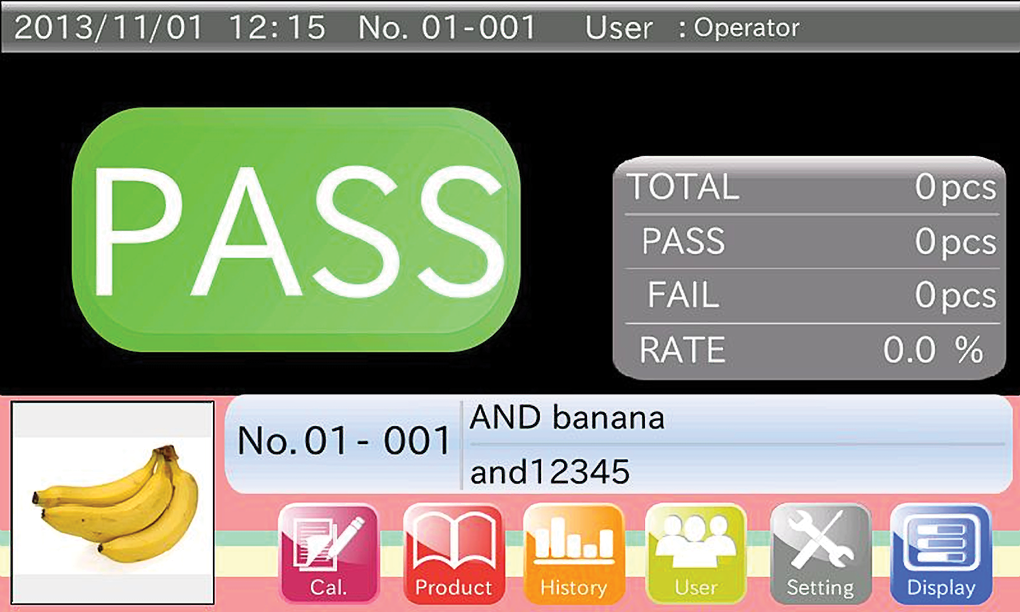
A common assumption about metal detectors is that the more sensitive it is, the more precise it will be. However, there’s more to it than simply choosing a detector with the highest sensitivity-levels. While sensitivity is important, veteran users understand that several other factors should also come into play when comparing metal detector units such as:
Stability
Top-quality metal detectors are stable metal detectors. The best detector units will be able to operate steadily without false rejects and erratic detections in real plant conditions. Adjustments – especially when attached to an automatic reject device – shouldn’t be a constant requirement.
User-Friendliness
Complex set-up procedures can often lead to incorrect parameter adjustments. The easier it is to initially set up the metal detector and adjust the settings without referring to the manual, the better.
Automated Monitoring
Metal detection systems that come with automated condition checking features improve uptime and production efficiency by reducing the need for scheduled testing. This system feature notifies users of potential system failure, allowing users to implement preventive measures instead of relying on reactive maintenance and constant testing.
Electronic Drift
A change in sensitivity, also referred to as “drift”, is caused by temperature variations combined with ageing electronic components over time. Electronic drift often affects stability which in turn can lead to false alarms or unwanted signals. The higher the level of sensitivity, the more important stability becomes. To minimise electronic drift, users should consider features like Quartz Frequency Control, Automatic Temperature Stability Control, and Auto Balance Control to ensure that the correct system sensitivities are maintained.
Repeatability
Getting detectors with a high level of repeatability ensures that products only have to undergo inspection once. In addition, reliable metal detectors will be able to properly identify metal contaminants and keep them from passing undetected during production.
PROTECTION AGAINST THE ENVIRONMENT
For industries with perishable products such as meat, poultry, and dairy, adhering to hygiene standards will be a number one priority within the facility.
Make sure to get a metal detector such as the AD-4971 Series that can withstand frequent deep cleaning and sterilization, as well as other harsh conditions. What’s great about the A&D Metal Detector is that it is suitable for direct food contact and offers a wash down rating for sanitary cleaning.
THE IDEAL CONVEYORIZED METAL DETECTOR DESIGN
If you’re getting a metal detector system with a conveyor belt that transports products through the detector, be sure to get one with fully welded structures that incorporate metal-free zones, insulated rollers and pulleys, and an insulated detector head mounting.
This prevents instability caused by eddy currents in a unit’s frame or static build up from the conveyor belt which interfere with sensitivity. Additionally, conveyor belting materials must be free of metals with contaminant-free joints and should not have anti-static belting materials.
STANDALONE HEADS
Customers sometimes will consider upgrading metal detector components.
If you are looking to replace an existing metal detector head to be fitted to an existing conveyor A&D can assist with their standalone head product lineup.
THE REJECT MECHANISM
A metal detector’s reject mechanism should be foolproof and able to reject contaminated products under any circumstance regardless of frequency and location within the item being inspected.
A&D has been providing industry-leading precision weighing and measurement equipment across the world for over 40 years. At A&D Inspection, you can rest easy knowing that each piece of equipment passes through the highest of quality standards at ISO 9001 certified facilities. To view A&D Inspection’s complete line of Metal Detectors and Accessories visit the website today and we’ll provide you with worry-free and convenient warranty services for guaranteed product performance and quality satisfaction.